The company is a leading supplier for responsible manufacturing solutions via industrial 3D printing technology. With their innovative 3D printers, they are leaders in technology and quality for high-end solutions in additive manufacturing (AM).
In additive manufacturing, material is applied layer by layer in precise geometric shapes based on a CAD model. In contrast, conventional manufacturing processes typically involve milling, carving or otherwise removing material to create an object. The terms 3D printing and additive manufacturing are often used synonymously. Strictly speaking, however, a distinction must be made: 3D printing is the more colloquial term. Additive manufacturing refers to the general manufacturing process – the production of objects by adding material – under which various production processes such as rapid prototyping, rapid tooling or mass customization can be subsumed.
Valve for Argon Gas Proves to be Critical Part of 3D Machinery
The industrial 3D printers manufactured by this company would not run as efficiently and smoothly without the addition of a valve. And in this particular case, the Pinch Valve for argon gas has been selected for it’s simple design and reliable function. The Field Service Engineer said:
“The Pinch Valves do their job well, we rarely have issues with them.”
The valve for argon gas assists with this application by sealing the main building area from the filtering system when the machine is not running, and allows waste to pass through when the system is running.
Pinch Valves used within this application: VMC80.03X.50G.30LX
VMC model, DN80, air operated, aluminium body, stainless steel threaded ends, black natural rubber sleeve.
Valve for Argon Gas Application Details
The media passing through the valves is nominally argon gas and small metal condensate at a pressure of 30-35mBar. There are two Pinch Valves per machine – One at the extraction from the process chamber and one on the return to the process chamber, from the filter system. When the machine is in use, the valve is normally open, and when the machine is at rest the valve is closed using 4 Bar air pressure. The valve opens at job start and closes at job finish. Jobs can be between 5 hours and 5 days long, depending on the customer.
The application consists of a simple circuit with a on/off/vent solenoid to control it, which is either fully open or fully closed.
Photos of the valves for argon gas installed within the 3D printing machines are not possible since they are enclosed within the housing of the system, but the company were able to supply a photograph of one of the valves fitted to pipework, ready to install.
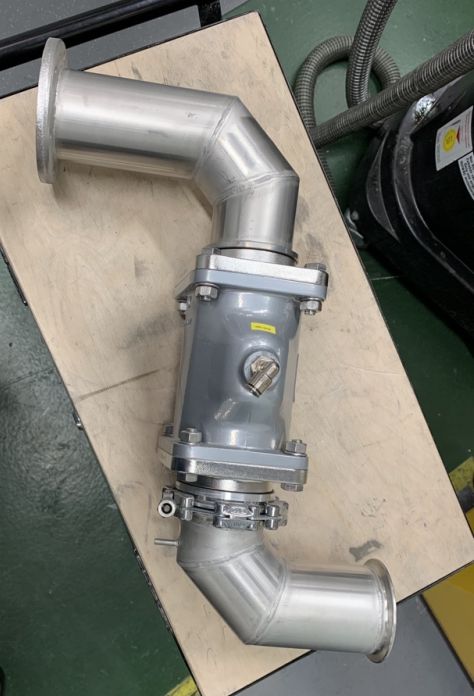
Experience with Pinch Valves for Argon Gas
The 3D printer manufacturing company have been using Pinch Valves for 15 years, if not longer. Their plans only date back 15 years but there were machines before this which likely used them.
Until recently, the sleeves inside the valves for argon gas were only replaced when they were worn and not opening/closing properly or bust. They were lasting up to 10 years in some cases. However, newer machines run hotter with more waste and we are finding they wear out more frequently. As such, newer machines are being replaced every 2 years now, with older machines being replaced every 5 years.
With the rubber sleeve being the only wearable part on these valves, and not being particularly expensive to replace, it gives them an excellent total cost of ownership. The sleeve inserts are also very easy to refit, especially with AKO UK’s fitting instructions and videos.
The company will be buying a reserve amount of Pinch Valves and spare sleeves to keep in stock for emergency failures and to reduce downtime.