A company manufacturing semi-automatic, submerged arc welding machines have started using AKO Pinch Valves on their welding flux application. After welding, the flux is transferred into a collection hopper and from there goes back to the welding torch.
Valves for Welding Flux Application
There are two collection points for the flux, and the Pinch Valves help to either select which point the company want to use, or alternate between the two in regular time intervals.
The flux is sucked from two flux trays using a vacuum pressure to the main recovery hopper. One pinch valve is installed on each tray, so they can open and close each side individually while the vacuum pump is running. Because the vacuum pressure can partially close the Pinch Valve from the inside, then AKO recommended piping the same vacuum pressure to the inlet of the Pinch Valve to equalize the pressure. See more on using a Pinch Valve with vacuum here.
The temperature of the welding flux media is normally just above 100’C, and the valve required for the application needed to be abrasion resistant as well as heat resistant. Therefore, AKO supplied a Pinch Valve for welding flux with an EPDM internal rubber sleeve which is rated to 120’C. The EPDM sleeve is also an excellent grade of durable rubber for this application, and like all of AKO’s Pinch Valve Sleeves, it opens & closes in the same elliptical position every time, ensuring a longer service life.
There are two Pinch Valves installed on this welding machine – one is normally open and the other is normally closed. Each valve performs 10-20 cycles per hour, and a pressure of 4-5 bars is used to close the valves for welding flux.
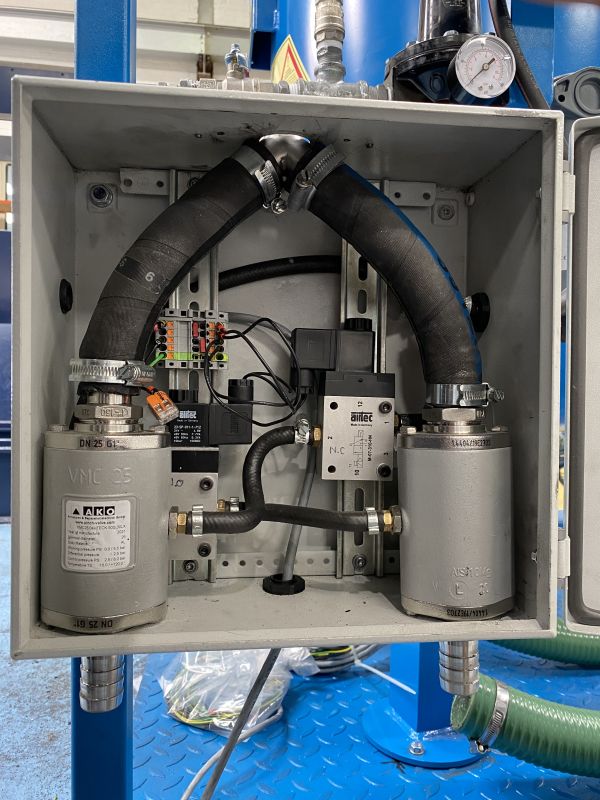
Pinch Valve used within this application – VMC25.04HTECK.50G.50
VMC model, air operated, EPDM rubber sleeve, stainless steel body, stainless steel BSP threaded end connections.
Pinch Valve Performance with Welding Flux
The company were experimenting with different solutions when they were building these welding machines. They had previously used butterfly valves and ball valves for welding flux, but told us that these valves didn’t work very well and that they had to be manually opened and closed.
The company found that the VMC Pinch Valve would be a good solution for the problem, and after the initial testing went very well, they were very happy with the Pinch Valve for welding flux and will be using them in all of their machines of this type going forward.
The company is an original equipment manufacturer, and so once they sell these welding machines on, they will be offering replacement sleeves as spare parts to their customers.