Machining 15 million brake discs every year to an industry leading standard, this company needs precision and reliability – which is why they are using Pinch Valves within their application.
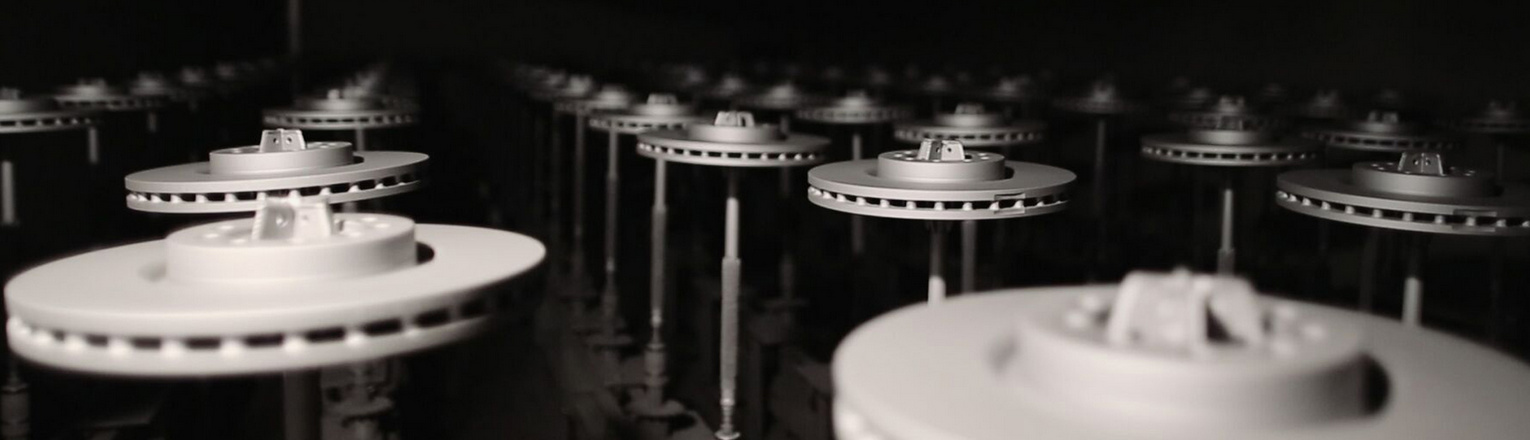
Valve for Compressed Air: How it Assists
The foundry where AKO’s Pinch Valves are installed has compressed air that is forced into a chamber, thus forcing sand into the required mould. Pinch Valve AKO5 (pictured) is used to hold the air in the chamber, then once the sand has been pushed around the mould the Pinch Valve is released and the compressed air is exhausted out through the Pinch Valve.
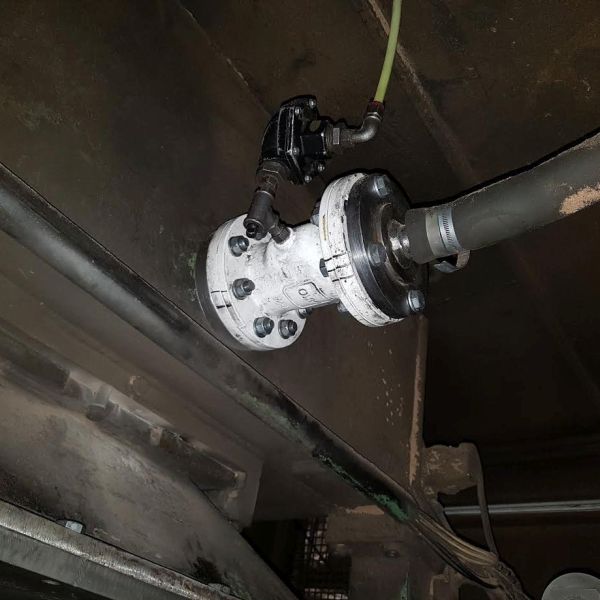
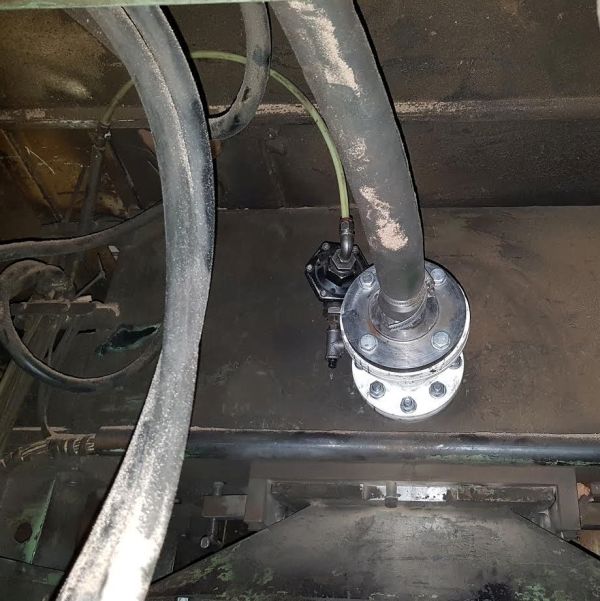
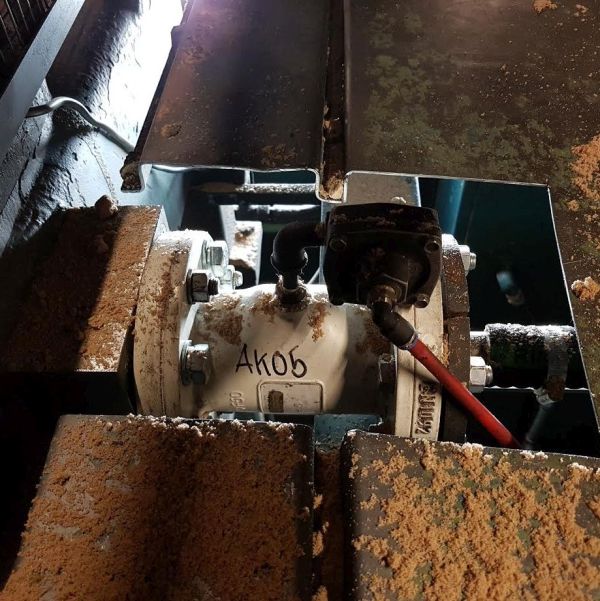
The compressed air that is being blown through the pipelines and the Pinch Valves is a pressure of 4.5 BAR. A compressed air pressure of 6.5 BAR is used to shut off the valves. The pneumatic Pinch Valves are open, and held closed when required, performing around 700 cycles per day. The core shop is run 24/7.
Pinch Valve used within this application: VF050.03X.31.30LA
VF model, air operated, aluminium body, aluminium PN10/16 flanges with mild steel bushings, natural rubber sleeve.
Customer Satisfaction
The company have been using Pinch Valves for compressed air from AKO UK for 15+ years. Steve, a maintenance worker from the company told us that they started using Pinch Valves as they were a more reliable product and reduced down time, compared to other valve types they were previously using. The non-clogging, no media build-up and no mechanical parts are just a few of the advantages of AKO Pinch Valves that this company relish in. (See more Pinch Valve advantages).
Steve also commented:
“I can certainly say your AKO UK’s help and delivery over the years have been excellent. We are very happy with the performance of your product.”
Maintaining Pinch Valves
The eliptical shaped body of AKO’s Pinch Valves uses less air consumption, and in turn helps the rubber sleeve to last longer with unbeatable lifetimes.
If the correct operating instructions and advice are adhered to, a user will get the absolute best performance from their Pinch Valve. The recommended differential pressure of 2-2.5 BAR is being correctly used at this foundry, and the temperature of the media passing through the valve is well within the maximum limit (Natural Rubber – max. 80°C). Therefore, the rubber sleeves are replaced very infrequently, sometimes just for a scheduled maintenance check.
The sleeve is the only wearable part that needs replacing on an AKO Pinch Valve – Another positive factor that this company enjoys.