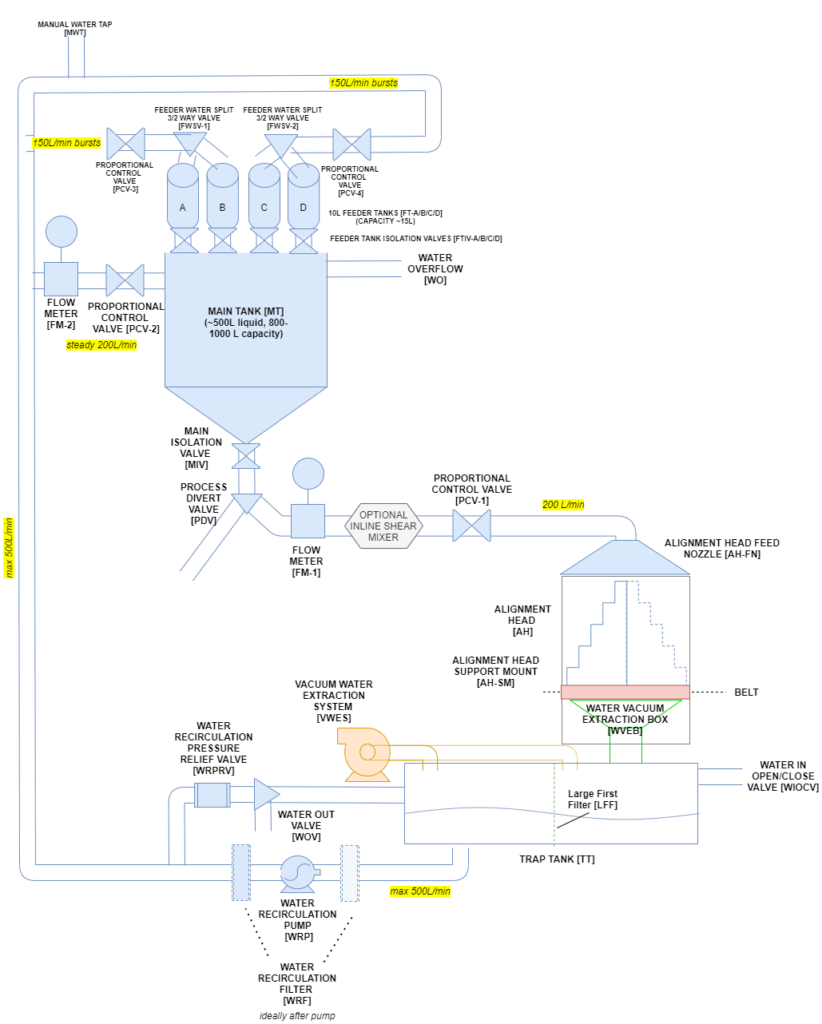
Set up of Valve Products Confirmed
The set-up would be a normal pinch valve, linked with a Proportional Control System (PCS) to control the air pressure. If the water / line pressure is 1.2 bar (absolute), so 0.2bar gauge, the sleeve works as a spring so it would require a pilot/air pressure of 3.2 bar to fully close. Using the PCS on a 4…20 mA signal would mean they would set the 4 mA signal to 0 BAR and the 20 mA signal to 3.2 BAR. Then adjusting the PCS signal between 4 and 20 mA would give different closing points of the Pinch Valve.
Valve for Carbon Fiber Recycling Results
“We couldn’t test the full flow rate through it as we don’t have our full system up yet but we partial closing / opening worked well by varying the pressure (I thought it would be much more abrupt). That gives us confidence going forward with the pinch valves.”
Pinch Valve used within this application – VMC50.03X.50F.50
VMC model, air operated, stainless steel body, Natural rubber sleeve, stainless steel PN10/16 flange connections.
The Project Coming Together
After discussing different options for valves during the R&D phase of the project and trialing Pinch Valves, the company had reached a stage where they were ready to source the parts they need for their big machine.
They decided to use AKO Pinch Valves from the VMC range with pressure switches (the same complete stainless flanged version that they trialed) for feeder tank output valves, and for the feeder tank output valves feedback system. The company will also be using the Proportional Control System fitted to a Pinch Valve to allow a percentage of air inside to partially close the sleeve.
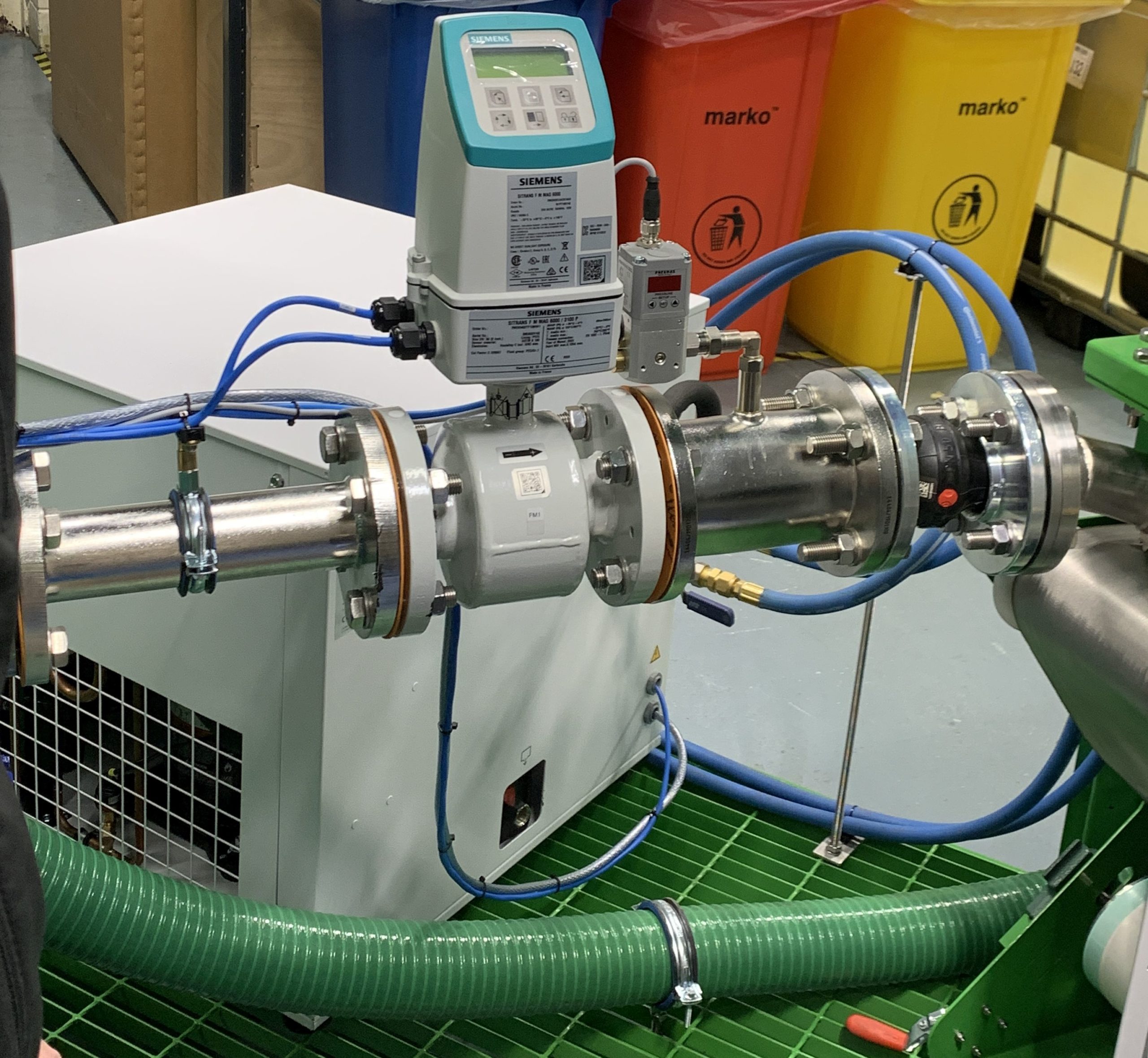
Pinch Valve for Carbon Fiber Recycling Success
After another 12 months AKO UK got back in touch with the company building this machine, who told us that the valve for carbon fiber is working well for them. They were having some issues but these were to do with pneumatic controller for the valve, not the valve itself. They contacted the manufacturer of the pneumatic controller who supplied them with a full manual for the device, which allowed them to set the parameters they needed to get the system operating within their expectation. This resolved the issues.