The products manufactured on site and supplied all over the world are camera lenses, contact lenses, lenses for prescription spectacles, and sun lenses.
AKO UK recently visited the manufacturing premises to see our products in action. The company have 8 lens polishing machines, all of which have two AKO Pinch Valves installed underneath. All machines are using DN15 valves from AKO UK’s VMP range, as well as one DN25 on one machine because the pipework is bigger.
Pinch Valve used within this application: VMP015.03XK.72 & VMP025.03XK.72
VMP model, air operated, black POM plastic body & BSP threaded ends, natural rubber sleeve.
The Operation of Lens Polishing Machines
A lens is placed onto a pad inside the polishing machine. Once the machine is turned on, a buffering pad moves down onto the lens, moving in a zigzag formation to clean it, buffering the surface whilst the lens polishing fluid is applied from two jets at the front of the machine. Once the machine is switched on, the air operated valves controls the flow of the fluid coming out of the jets as per below.
Valves for Lens Polishing Fluid in more detail
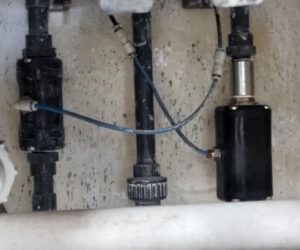
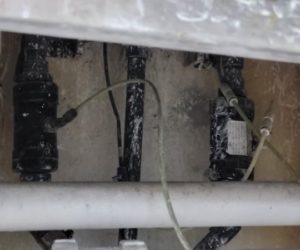
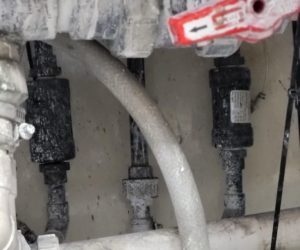
The purpose of the polishing fluid which is ambient temperature is of course to clean and polish the lens, but also to stop the pad from overheating, and to smooth the lens out.
Once the polishing process is finished, any excess waste travels down a waste pipe and into a bucket underneath the machines.
Experience with Valves for Lens Polishing Fluid
Hundreds of cycles are performed by the valves for lens polishing fluid per day, whilst hundreds of lenses are manufactured and polished.
Since the valves were installed in 2011, the company had never needed to replace a valve or sleeve within this time (current year when writing is 2023). Until recently, when one of the valves failed due to a split in the sleeve. The sleeve had split halfway along, where it had been compressing over time. However, this was caused by an accidental foreign body within the pipeline, and not through any fault of the valve.
The company decided to change the sleeves in all valves for lens polishing fluid on the machines at once, so that they were all the same age. They also decide not to keep stock of any spare sleeves. Partly, because it is so easy to obtain replacements from AKO UK with next day delivery, and also because if the current sleeves do not need replacing for years then any sleeves kept in stock will have a reduced shelf life.
The valves were already on the machines when the lens manufacturer obtained them from an Original Equipment Manufacturer in the US.