The packaging machines that the Pinch Valves from AKO UK are used on, are suited to a wide range of films with 3 or 5 layers and combine high output rates with outstanding film quality. Adapted for optimised extrusion, the machines deliver excellent melt quality, have a cooling ring and profile control to ensure the perfect film quality at maximum output and best film tolerances, full integration of all machine components, a long collapsing unit for excellent flatness, and intelligent automation modules for economic production.
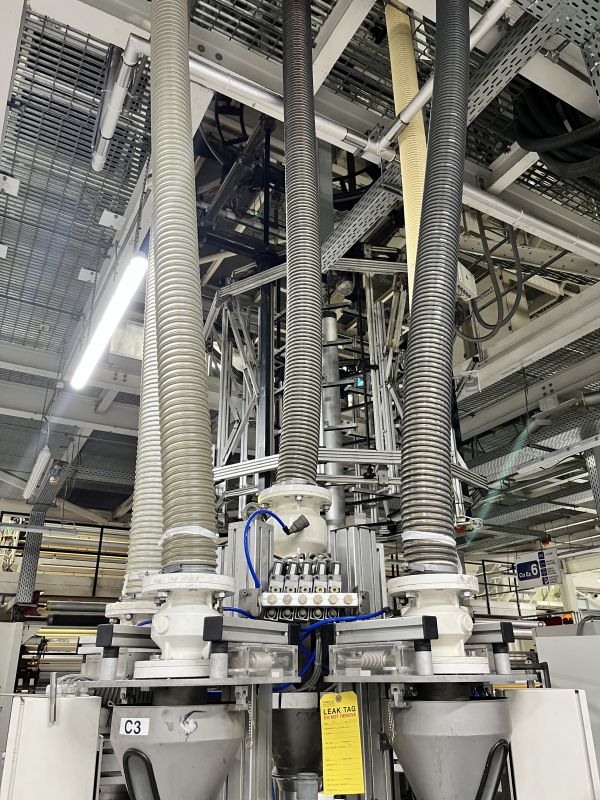
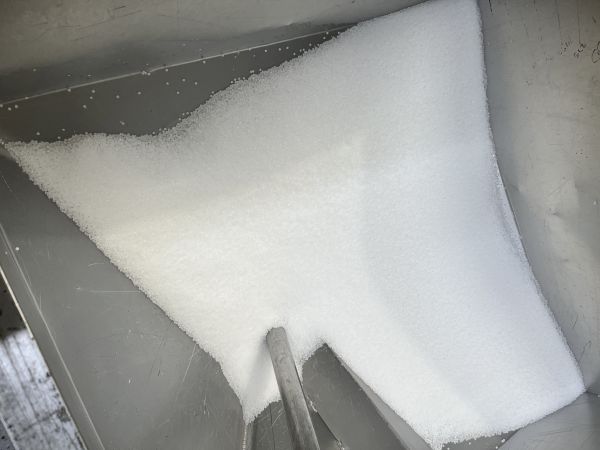
Other packaging machines on the same site with AKO Pinch Valves installed, use high performance thick PE-HD liner films and 11 layer barrier films. Short start-up and changeover times reduce the use of raw materials and significantly reduce the amount of waste, while maintaining film qualities. This specific machine is the best choice for the best blown film quality with maximum output rates and optimum material efficiency.
On the note of efficiency, the Pinch Valve helps to make a noticeable difference with the production and smooth effectiveness on the machines.
Valves for Packaging Machinery Application Details
There are multiple machines varying in size at this site, therefore a range of air operated valve sizes are used to allow a measured amount of resin in to a weigh pan. The polyethylene resin passing through the valves is ambient in temperature, and gravity fed through.
Pinch Valve used within this application: VF050.03X.31.30LA, VF065.03X.31.30LA & VF080.03X.31.30LA
VF model, air operated, aluminium body, aluminium flanges PN10/16 with mild steel bushing contact parts, natural rubber sleeve.
Each valve is positioned on the blown film extrusion line, and normally closed. 2.5 bar is the amount of air used to close the valves, which is the correct recommended differential pressure. (2.5 bar above the line pressure is recommended to fully close off the valves, and the media is gravity fed in this application). Each valve performs up to 250 cycles per day.
Expectant Lifetime of Valves for Packaging Machinery
The Engineering Team Leader at the blown film extrusion manufacturing site told us at AKO UK that it is hard to say how often the rubber sleeve is replaced. They measure the time taken to dispense, and change the sleeves when the amount of time goes over 12 seconds. Estimated sleeve replacement time would be every 3 years.
As shown above, the tiny polyethylene resin balls that pass through the valve are smooth and rounded, so not abrasive to the rubber sleeve which closes tightly around them to fully shut off the flow. Since there is limited pressure being used with the resin being gravity fed, this will also have a good impact on the sleeve lifetime.