“As the Production Engineering Manager of our company, I am really impressed with the stainless steel construction of the AKO VMC type Pinch Valves, as an older aluminium bodied pinch valve by another manufacturer that we were using previously continued to become damaged by the fragments of welding flux that is used in our application. AKO’s stainless steel pinch valve is much more robust and so much easier to install and maintain.”
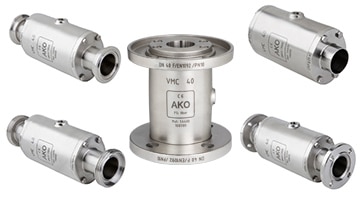